Crusher Level Measurement and Feed Control: The Importance of Accurate Radar Level Measurement in the Mining Process
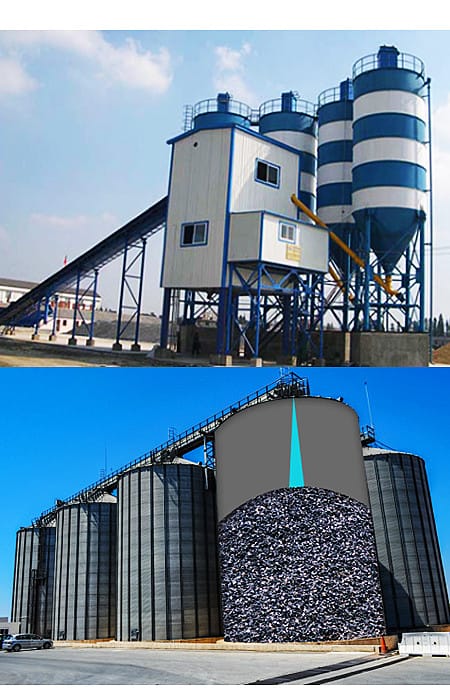
Crushing is an essential process in the mining industry, where ores are extracted and processed to create various materials that are needed for infrastructure development, manufacturing, and other purposes. The crushing process involves reducing the size of large rocks, ores, and other materials that are initially too big to be easily handled or transported. However, crushing also poses various challenges, such as dealing with intense dust generation, which can lead to inaccurate measurement and poor feed rate control.
To ensure reliable measurement and feed rate control in crushers, it is crucial to use accurate and reliable level measurement technology that can withstand the harsh conditions of the mining process. Radar level measurement is an excellent solution for contactless level measurement in crushers, providing a reliable and accurate measurement of the level of solids even in dusty environments.
Radar level measurement is based on non-contact technology, which can measure the distance between the sensor and the material surface without physical contact or interference with the process. Not only is radar level measurement contactless, but it is also highly accurate, providing precise measurements of the level of solids in the crusher. This accuracy is essential for ensuring that the crusher is running efficiently and effectively, with sufficient material being fed into the crushing chamber without overloading the machine.
One of the main advantages of using radar level measurement in crushers is its ability to overcome the challenges posed by intense dust generation. Dust is a significant problem in the crushing process, as it can interfere with the accuracy of the measurements and the performance of the equipment, leading to poor feed rate control and reduced efficiency. Radar level measurement uses high-frequency signals that can penetrate through dust, providing a reliable and accurate measurement of the level of solids.
Another benefit of radar level measurement for crushers is its ability to provide continuous measurement, enabling users to monitor the level of material in the crusher in real-time. This allows for better feed rate control, ensuring that the crusher is being fed with the right amount of material at all times, avoiding the risks of overloading or underloading the machine. This level of control is essential for optimizing the crushing process, reducing downtime, and improving overall performance.
Overall, radar level measurement is an excellent solution for contactless level measurement in crushers, providing accurate and reliable measurement of the level of solids, even in dusty environments. This technology is essential for ensuring efficient and effective crushing processes, reducing downtime, and improving overall performance. For mining and other heavy industries, investing in accurate and reliable level measurement technology is essential for maximizing productivity and profitability.
In conclusion, the use of radar level measurement technology is crucial in the mining process, particularly in the crushing stage for optimal machine performance. The dusty environment that is prevalent in the crushing process makes it difficult to obtain accurate measurements, but radar level measurement overcomes this challenge, providing reliable and contactless measurements. To optimize the crushing process in mining, it is important to invest in accurate level measurement technology like radar level measurement that provides continuous measurements and feed rate control, enabling the crusher to operate efficiently, reducing downtime, and the risk of equipment failure.